What is the 5S Methodology?
Boosting Business Basics: A Small Business Guide to all things Lean and OpEx
This blog series explores key concepts in Operational Excellence (OpEx), Lean methodology, and Continuous Improvement (CI) for small businesses. It covers topics such as Value Stream Mapping, the 5S methodology, the PDCA cycle, Kaizen, and Standard Work, providing practical insights to help small businesses enhance efficiency, reduce waste, and deliver high-quality products or services.
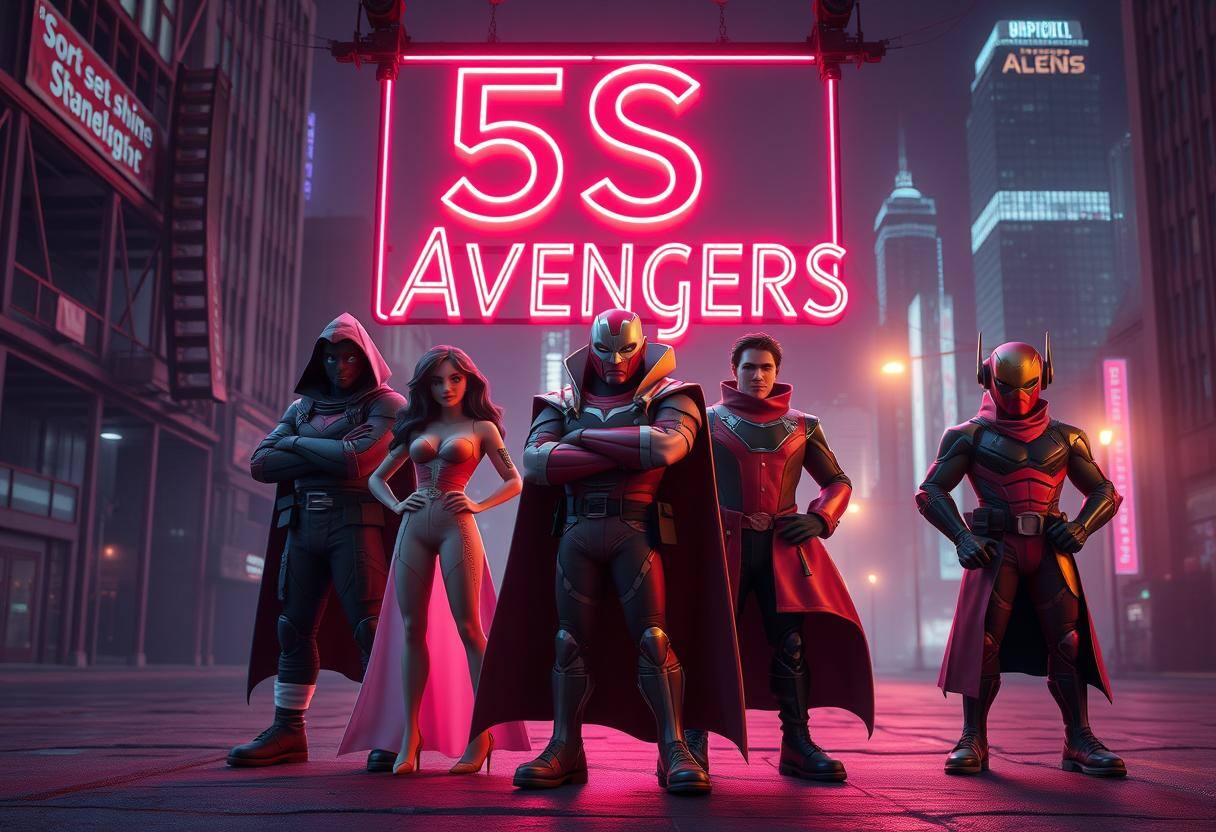
Blog 5: What is the 5S Methodology?
The 5S methodology is a Lean tool that helps businesses create a well-organised, efficient, and safe workplace. For small businesses, 5S can lead to improved productivity, reduced waste, and a more pleasant working environment.
- Sort (Seiri)
The first step in 5S is to sort, or Seiri, which means to remove unnecessary items from the workplace. This includes anything that isnot used regularly, is broken, or is simply taking up space. Sorting through inventory and removing outdated or unpopular items can free up valuable space and reduce clutter, making it easier to find the items you need. In a small craft store, for example, sorting through inventory can help identify items that are not selling well, allowing the owner to focus on stocking more popular items. This not only frees up space but also reduces the risk of having to deal with excess inventory that may expire or become outdated. A small office could sort through paperwork and files to remove any that are no longer needed, freeing up desk space and making it easier to find important documents. - Set in Order (Seiton)
Once you've sorted through your workspace, the next step is to set in order, or Seiton. This means arranging necessary items so that they are easy to access and use. By organizing tools and materials in a logical way, you can reduce the time it takes to find what you need, improving efficiency and reducing wasted time. A small repair shop could organize tools by frequency of use, ensuring that the most commonly used tools are always within reach. This reduces the time spent searching for the right tool and
allows technicians to focus on their work. A small retail store could organize its merchandise by category, making it easier for customers to find what they are looking for, improving the shopping experience and boosting sales. - Shine (Seiso)
The third step in 5S is Shine, or Seiso, which means to clean the workspace and equipment regularly. A clean and organised workspace not only improves aesthetics, but it also helps prevent accidents and improves
the overall safety of the workplace. Regular cleaning can also help identify any potential problems with equipment or facilities, allowing for prompt maintenance and repairs. A local restaurant could establish a
daily cleaning schedule to keep the kitchen spotless, reducing the risk of contamination and speeding up service. A small manufacturing plant could implement a regular cleaning schedule for their machines, ensuring that they are functioning at their peak performance. - Standardize (Seiketsu)
The fourth step in 5S is Standardise, or Seiketsu. This means developing standards and procedures to maintain organisation and cleanliness. Standardizing processes can ensure that everyone in the workplace
understands and follows the same procedures, leading to greater consistency and efficiency. A boutique clothing store might standardise folding techniques and displays to ensure a consistent customer experience. This not only creates a more visually appealing environment but also
makes it easier for employees to manage the store's inventory. A small construction company could standardize the way they store tools and materials, ensuring that everyone is on the same page and that the
workspace is always organized and safe. - Sustain (Shitsuke)
The final step in 5S is Sustain, or Shitsuke. This means maintaining the standards and procedures established in the previous steps. This is an ongoing process that requires commitment from everyone in the workplace. By establishing a culture of continuous improvement, businesses can ensure that 5S principles are ingrained in their daily operations. A small bakery could implement a daily checklist for their
employees to follow, ensuring that the bakery is always clean, organised, and ready for business. A small software development company could hold regular meetings to review their processes and identify areas for improvement, ensuring that their work environment is always efficient and productive.
Implementing 5S can help small businesses create a more efficient and organised work environment, reducing time wasted on searching for tools or materials and improving overall productivity. For example, a small catering
company could use 5S to organise their kitchen and prep areas, reducing prep time and improving service speed. By adopting the 5S methodology, small businesses can benefit from a more organized, efficient, and safe work
environment, leading to increased productivity, reduced waste, and a happier and more engaged workforce.