What is Lean, and Why Does It Matter?
Boosting Business Basics: A Small Business Guide to all things Lean and OpEx
This blog series explores key concepts in Operational Excellence (OpEx), Lean methodology, and Continuous Improvement (CI) for small businesses. It covers topics such as Value Stream Mapping, the 5S methodology, the PDCA cycle, Kaizen, and Standard Work, providing practical insights to help small businesses enhance efficiency, reduce waste, and deliver high-quality products or services.
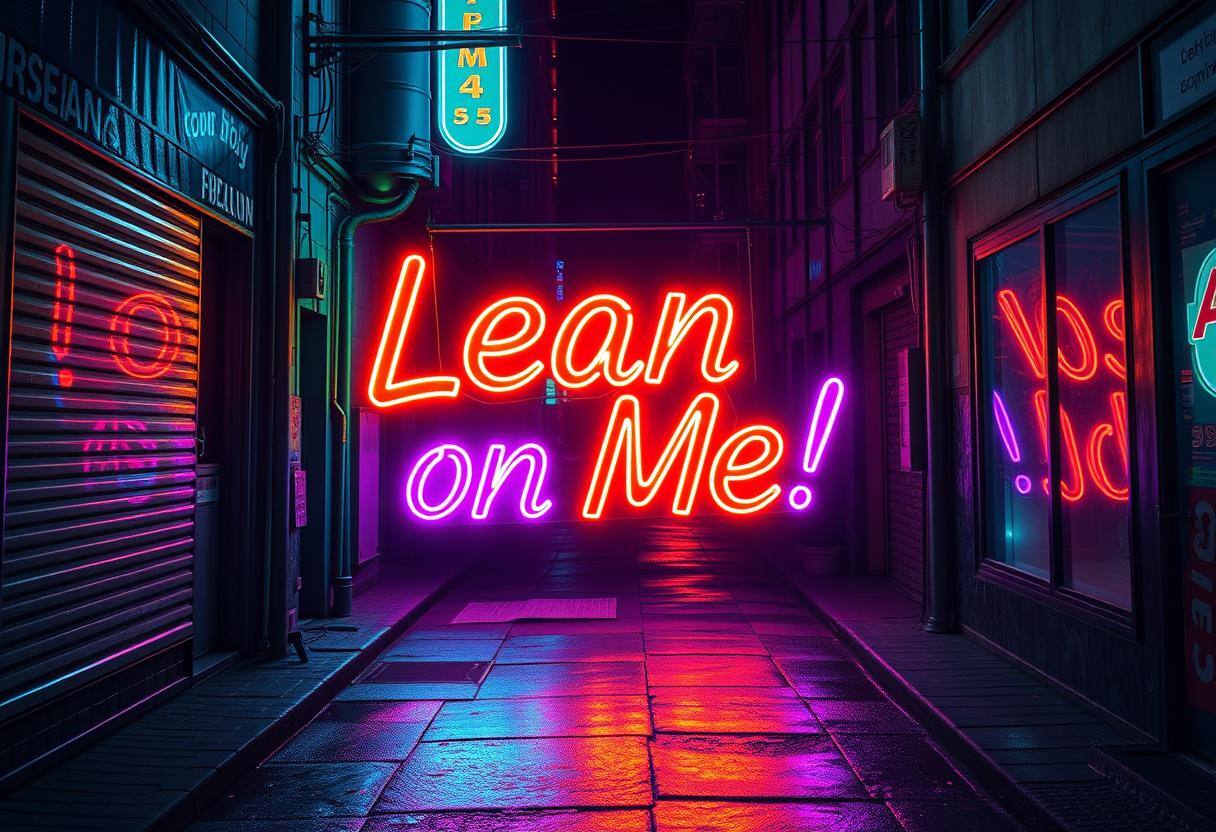
Blog 2: What is Lean, and Why Does It
Matter?
Lean is a methodology that originated in the manufacturing industry but has since been adapted across various sectors, including small businesses. At its core, Lean is about eliminating waste—anything that doesn't add value to the customer—and optimising processes to improve efficiency
- Value
Define what value means from the customer's perspective and focus efforts on delivering it. A small landscaping business, for instance, could focus on customer value by offering personalised
garden maintenance plans based on individual customer needs rather than a one-size-fits-all service. - Value Stream
Map out all the steps that bring a product or service from conception to customer delivery, identifying and eliminating waste. For example, a local café might map out the steps from ordering supplies to serving the customer, identifying areas where delays or excess inventory can be reduced. - Flow
Ensure smooth progression of work processes to avoid bottlenecks and interruptions. A small print shop could reorganise its workflow to ensure that print jobs move seamlessly from design to production, reducing waiting times and improving turnaround. - Pull
Create products or services based on customer demand rather than forecasting, reducing excess inventory and overproduction. A small artisanal bakery could switch to a pre-order system to ensure that every baked item is sold, reducing waste and increasing freshness. - Perfection
Strive for continuous improvement in all areas of the business. This could mean a small car repair shop continually refining its diagnostic procedures to reduce the time cars spend in the shop, thereby increasing customer satisfaction and shop throughput
For small businesses, Lean can lead to faster turnaround times, reduced costs, and a better overall customer experience. A local marketing agency, for example, might use Lean to streamline its project management process, ensuring every step from client briefing to campaign launch adds value and is performed efficiently.