Demystifying the PDCA Cycle (Plan-Do-Check-Act)
Boosting Business Basics: A Small Business Guide to all things Lean and OpEx
This blog series explores key concepts in Operational Excellence (OpEx), Lean methodology, and Continuous Improvement (CI) for small businesses. It covers topics such as Value Stream Mapping, the 5S methodology, the PDCA cycle, Kaizen, and Standard Work, providing practical insights to help small businesses enhance efficiency, reduce waste, and deliver high-quality products or services.
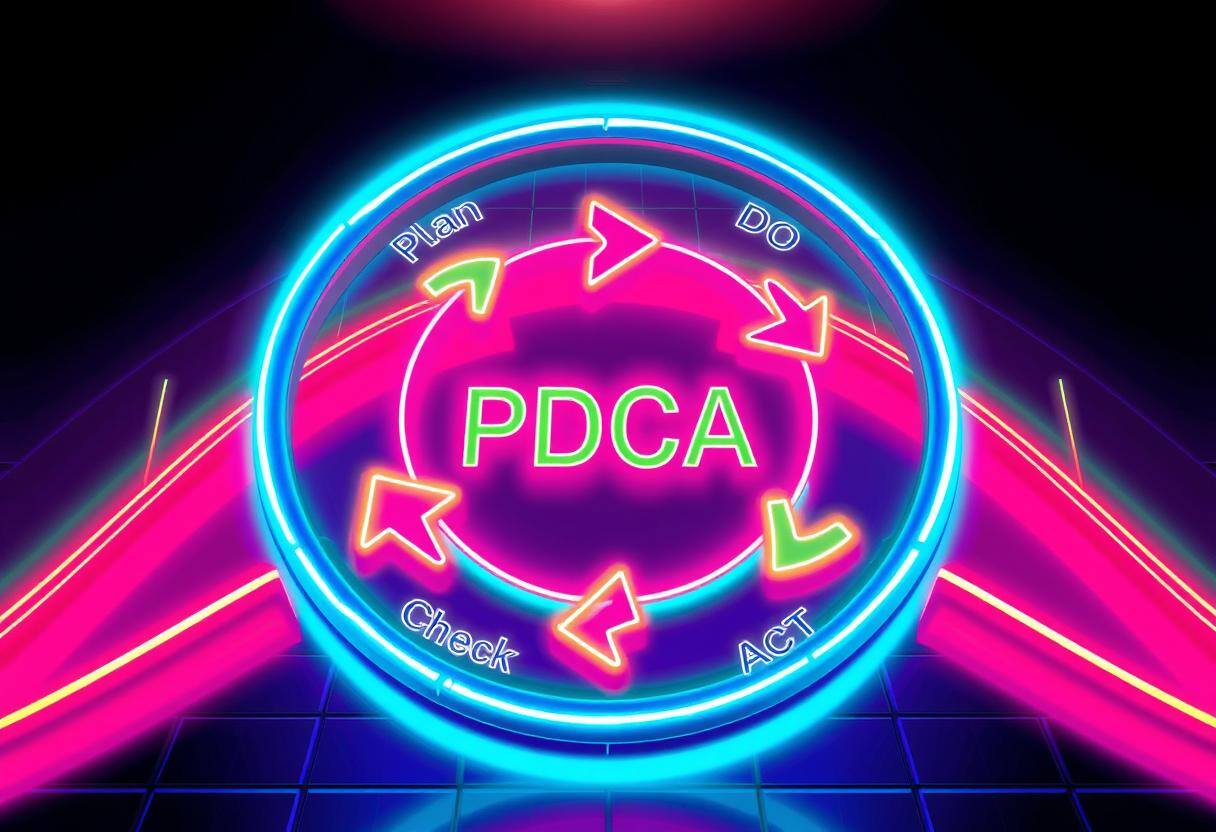
Blog 6: Demystifying the PDCA Cycle (Plan-Do-Check-Act)
The PDCA Cycle, also known as the Deming Cycle, is a four-step process used for continuous improvement in businesses of all sizes. It provides a straightforward framework for testing changes on a small scale before implementing them more broadly.
Plan
Identify a problem or opportunity for improvement and develop a plan to address it. A small boutique might plan to reduce customer wait times by rearranging the checkout area to be more efficient.Do
Implement the plan on a small scale to test its effectiveness. The boutique could pilot the new checkout process during off-peak hours to see if it reduces wait times.
Check
Review the results of the test to see if the desired improvement was achieved. After the pilot, the boutique could compare customer wait times before and after the change to assess its impact.
Act
If the plan was successful, implement it on a larger scale. If not, refine the plan and repeat the cycle. If successful, the boutique would roll out the new process storewide; if not, they would gather feedback and tweak the approach.
For small businesses, the PDCA Cycle offers a practical way to test and implement changes systematically, reducing risk and enhancing the effectiveness of improvement efforts. For example, a local gym could use PDCA
to test new class schedules to see which times attract the most attendees.