GE's Lean Six Sigma Transformation
Lean Legends: Landmark Lessons in Operational Excellence with Leon from OpX
Today Operational Excellence (OpEx), Continuous Improvement (CI), and Lean methodologies have become critical for companies striving to stay competitive. This blog series dives into the defining moments and pivotal transformations that have shaped industries worldwide. In each post, we uncover the stories behind iconic implementations of Lean principles, where visionary leaders and relentless teams turned challenges into triumphs. These are not just case studies; they are blueprints for success, offering powerful insights into how operational excellence can drive extraordinary results. Join us as we explore the legends of Lean and the lessons they offer for today’s fast-paced world.
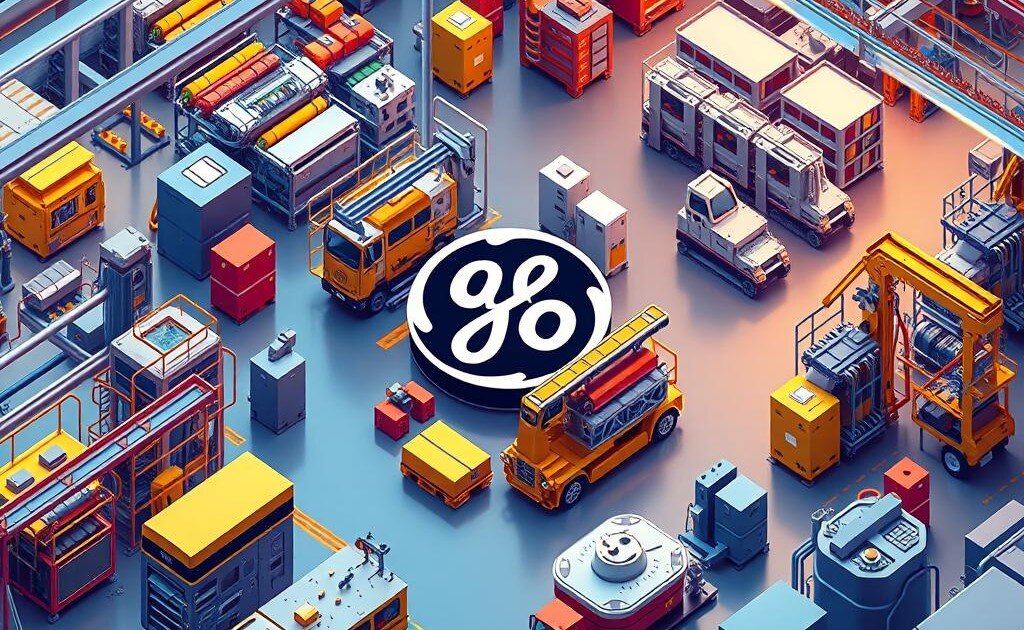
Blog 3: GE's Lean Six Sigma Transformation
In today's competitive business environment, operational efficiency and product quality are vital for success. General Electric (GE) is a prime example of how Lean Six Sigma can transform a company. During the 1990s, under CEO Jack Welch's leadership, GE embarked on a comprehensive Lean Six Sigma implementation across all its business units.
By integrating Lean's focus on waste reduction with Six Sigma's emphasis on reducing defects, GE achieved significant process improvements, cost savings, and enhanced product quality. The transformation led to billions
in savings and a reinforced competitive edge. GE was able to streamline operations, eliminate wasteful practices, and ensure consistently high-quality products across its diverse portfolio.
The results were truly remarkable. Lean Six Sigma allowed GE to become more agile, responsive, and customer focused. Processes that had historically been plagued by delays, errors, and excessive costs were optimised, leading to faster turnaround times, lower expenses, and higher customer satisfaction. This, in turn, enabled GE to better serve its clients and outpace its competitors in the market.
GE's story highlights the power of Lean Six Sigma in today's business environment, where efficiency and quality are paramount. By embracing a culture of continuous improvement and empowering employees to identify and
solve problems, GE was able to transform itself into a leaner, more competitive organisation that could thrive in an increasingly challenging global landscape.